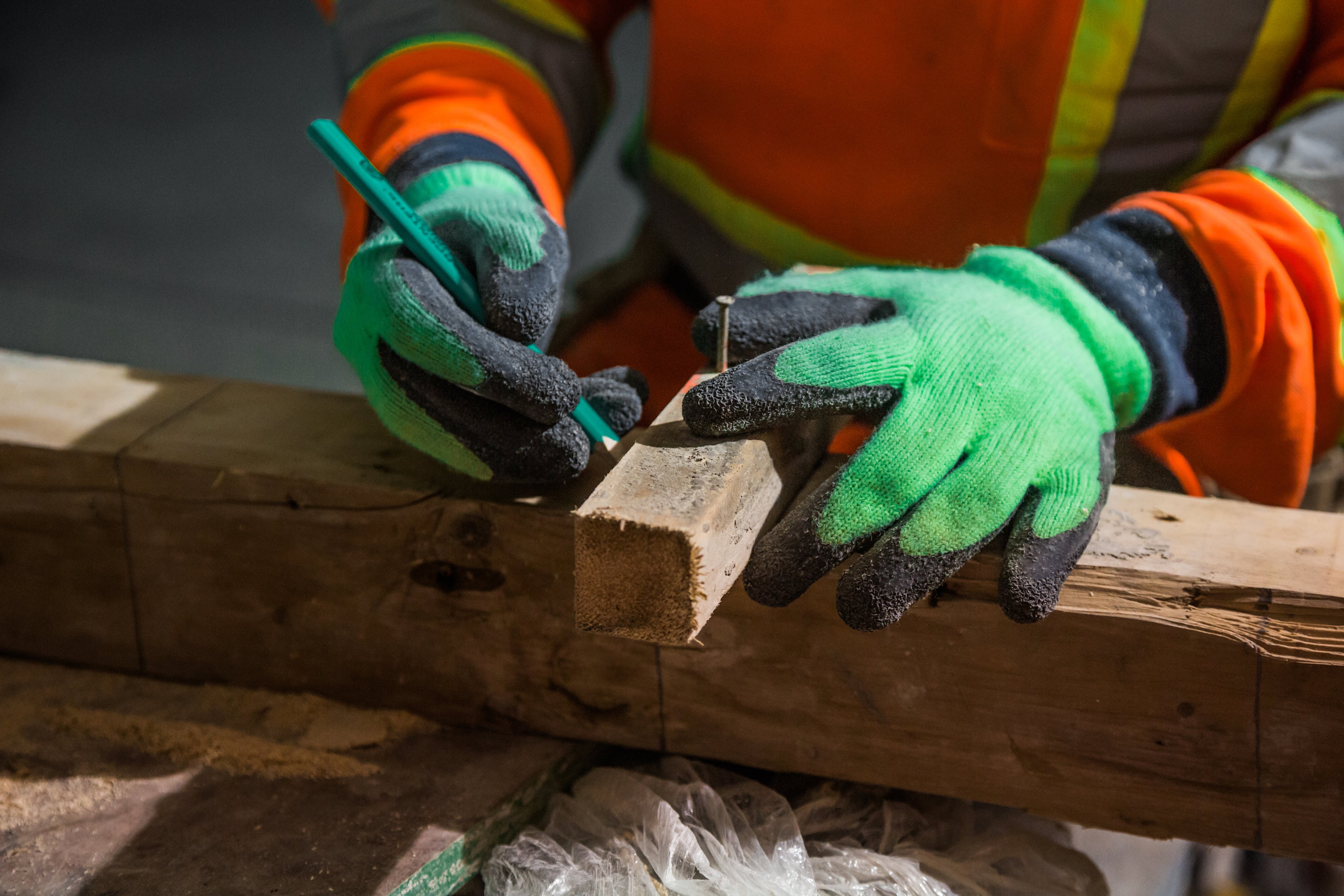
Comprehensive Glove Safety Audit
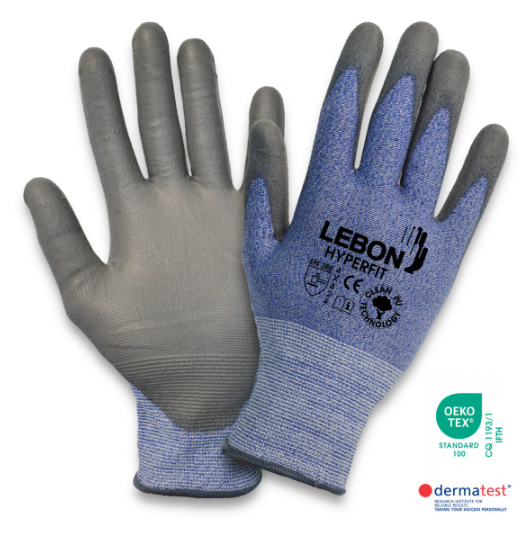
Protecting Hands & Enhancing Safety with a Glove Audit
Hand injuries are among the most common workplace incidents making proper glove selection essential for safety compliance & efficiency. Dalton Safety’s Glove Audit helps businesses assess risks, streamline glove usage & ensure employees are equipped with the best protective gloves for their tasks.
Our Glove Audit Process
Stage 1: Identify the Hazard & Workplace Risks
We conduct a site assessment to evaluate users' environments, tasks & hazards. We review glove use ensuring correct sizing suitability & compliance with EN safety standards.
Who is at Risk?
- Maintenance workers
- Contractors
- Drivers
- Machine operators
- Assembly workers
- Visitors
Significant Hazards
- Chemical exposure
- Sharp object handling
- Heat & cold risks
- Electrical hazards (ESD Atex)
- Wet greasy or oily conditions
Stage 2: Selecting the Right Glove
Using the data collected we create a detailed report outlining hazards glove requirements & recommendations for improvement.
Key Considerations
- Glove coating:
- Nitrile – Protection against grease oils & many solvents
- PU (Polyurethane) – Ideal for dry work requiring dexterity & grip
- Glove fit & comfort
- Compliance with industry standards
- Yearly glove expenditure & injury records
Stage 3: Presenting a Solution
We present a full report to stakeholders outlining findings & recommended glove alternatives including features benefits & compliance with EN standards. Approved solutions proceed to controlled trials.
Stage 4: Glove Evaluation Test
We provide glove samples to employees for testing ensuring correct sizing fit & industry standard compliance. Users complete evaluation forms covering:
- Dexterity & grip
- Comfort & fit
- Longevity & durability
Once trials are complete feedback is analysed with the safety team to confirm the best solution or make adjustments.
Benefits of Our Glove Audit
-
Reduced Workplace Injuries
Proper glove selection minimises risks from cuts, abrasions & chemical exposure ensuring employee safety.
-
Improved Compliance & Due Diligence
Our audit ensures gloves meet EN safety standards reducing liability & enhancing workplace safety policies.
-
Cost Savings & Efficient Glove Management
By consolidating glove usage & selecting the best-fit products businesses reduce waste & lower long-term costs.
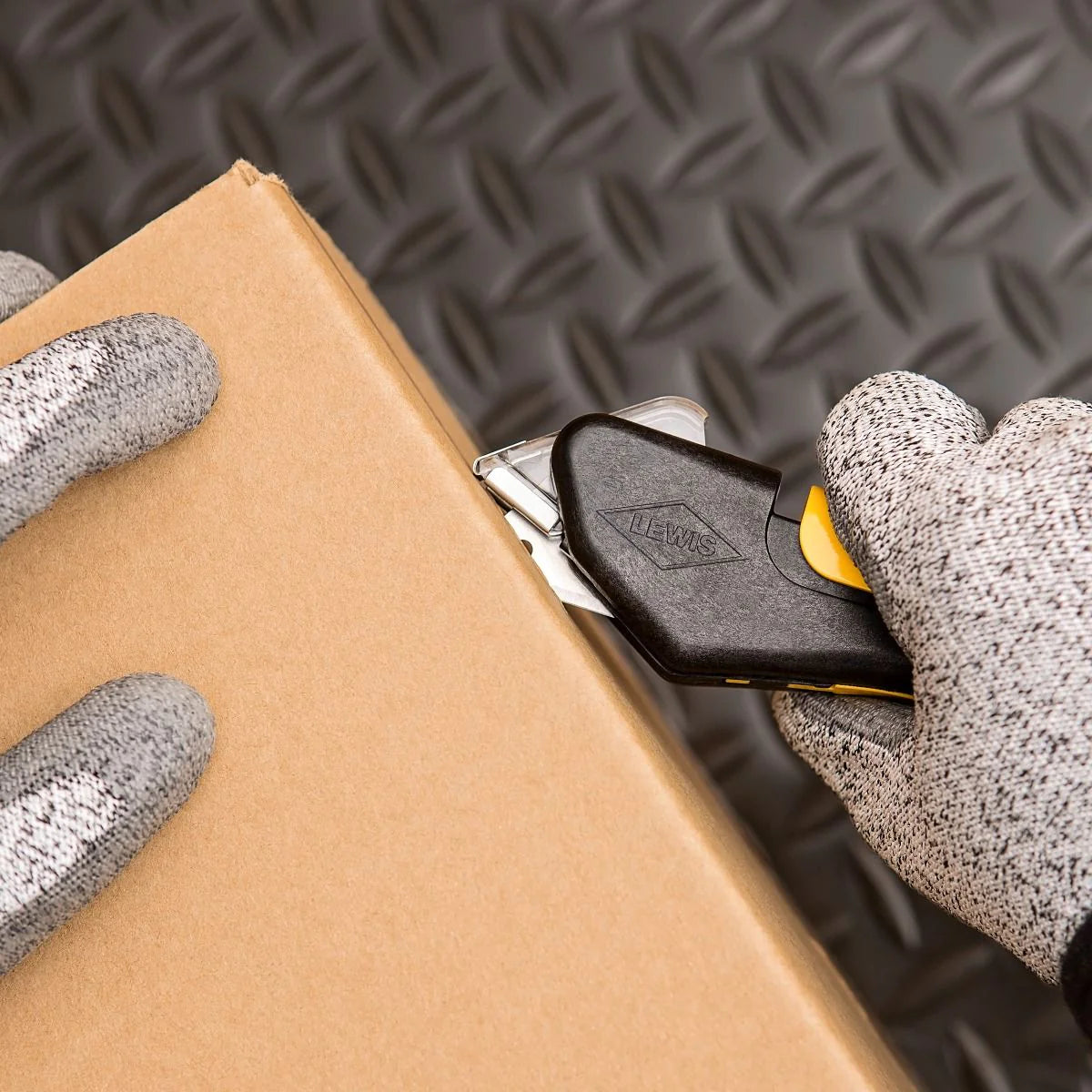
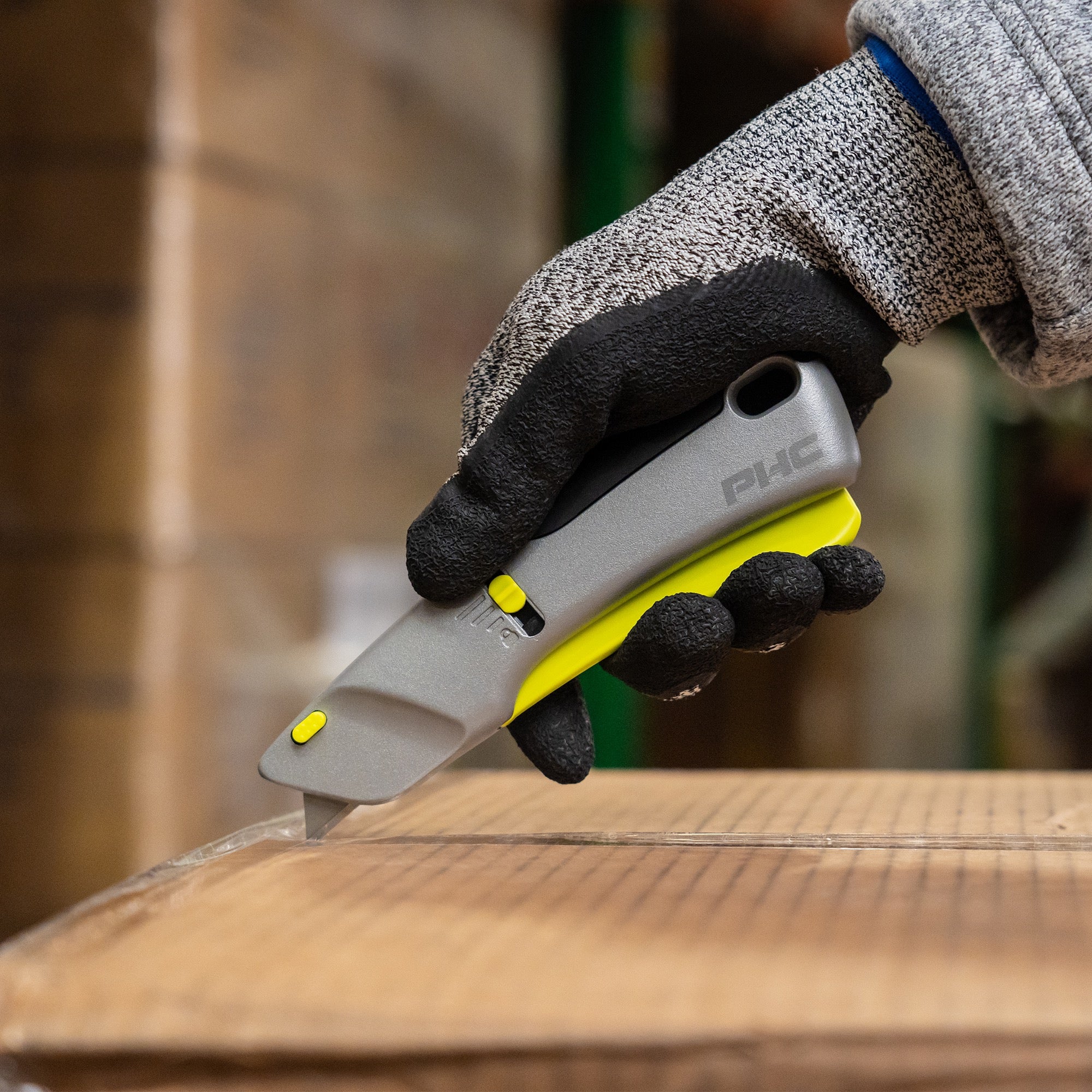
Book a Glove Audit
Ensure your employees have the right protective gloves for every task. Book a Glove Audit with Dalton Safety today & enhance workplace safety compliance & efficiency.