
Comprehensive Knife Safety Audit
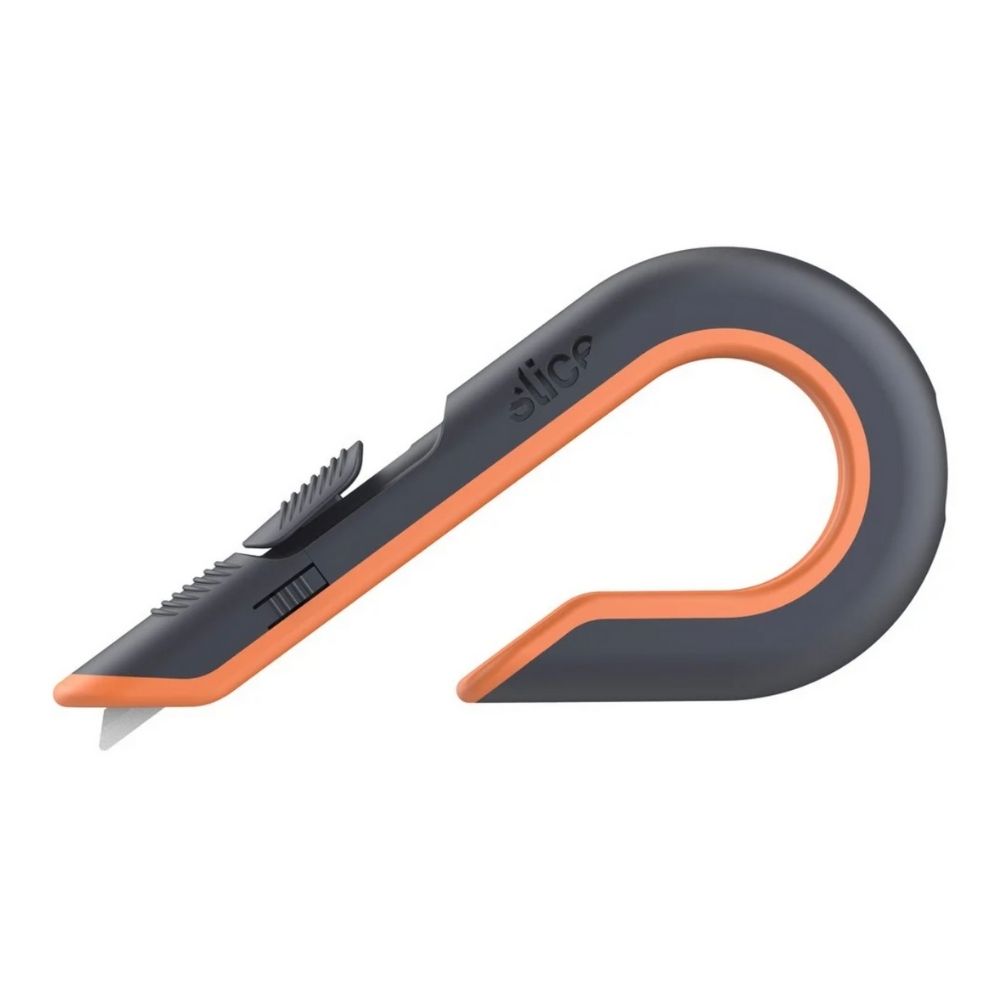
Reducing Risk, Enhancing Efficiency: Your Knife Safety Audit
At Dalton Safety, we understand that cutting tools are an essential part of many workplaces, but improper knife use and outdated tools can pose serious safety risks. Our Knife Audit is designed to improve safety, efficiency and cost effectiveness by assessing your existing cutting tools, identifying potential hazards and providing actionable solutions.
Our Knife Audit Process
Define the Objective
We start by understanding your business needs, whether it’s reducing workplace injuries, increasing efficiency or improving cost management of cutting tools.
Assessment of Current Cutting Tools
Our experts evaluate all cutting tools in use, from retractable and fixed blade knives to specialty cutting tools, ensuring a comprehensive audit.
Identification of Knife Types
We categorise each cutting tool by type and application to understand usage patterns and assess whether the right tools are being used for the right tasks.
Evaluation of Knife Condition
We inspect knives for wear, damage and dullness, identifying tools that require maintenance or replacement to maintain optimal performance.
Safety Analysis
We analyse safety features such as blade locking mechanisms, handle ergonomics and overall design to identify potential hazards and ensure compliance with workplace safety standards.
Usage Patterns & Handling Procedures
We assess how frequently each tool is used and review existing knife handling, storage and disposal protocols to align with industry best practices.
Cost Efficiency Examination
We calculate the total cost of ownership, factoring in purchase prices, maintenance and replacement expenses, to identify cost saving opportunities.
Recommendations & Solutions
Based on our findings, we provide actionable recommendations, from upgrading to safer models to implementing best practices and employee training programs.
Implementation Plan
We collaborate with your team to develop a phased action plan tailored to your budget and operational needs, ensuring seamless implementation of recommended changes.
Training & Education
We conduct training sessions to reinforce safe knife handling techniques, proper maintenance and best practices, helping reduce workplace injuries.
Follow Up & Monitoring
We schedule follow up audits to track progress, address emerging concerns and ensure continuous safety improvements.
Documentation & Reporting
A detailed report is provided, documenting findings, recommendations and progress over time, ensuring transparency and compliance.
Benefits of Our Knife Audit
-
Enhanced Workplace Safety
By identifying and eliminating unsafe practices and outdated cutting tools, we help reduce workplace injuries and create a safer working environment.
-
Increased Efficiency & Productivity
Optimised cutting tools and proper training lead to smoother workflows, reducing downtime and improving overall operational efficiency
-
Cost Savings & Long Term Value
Our audit identifies cost effective strategies, such as proper maintenance, improved purchasing decisions and reducing unnecessary replacements, to save your business money.
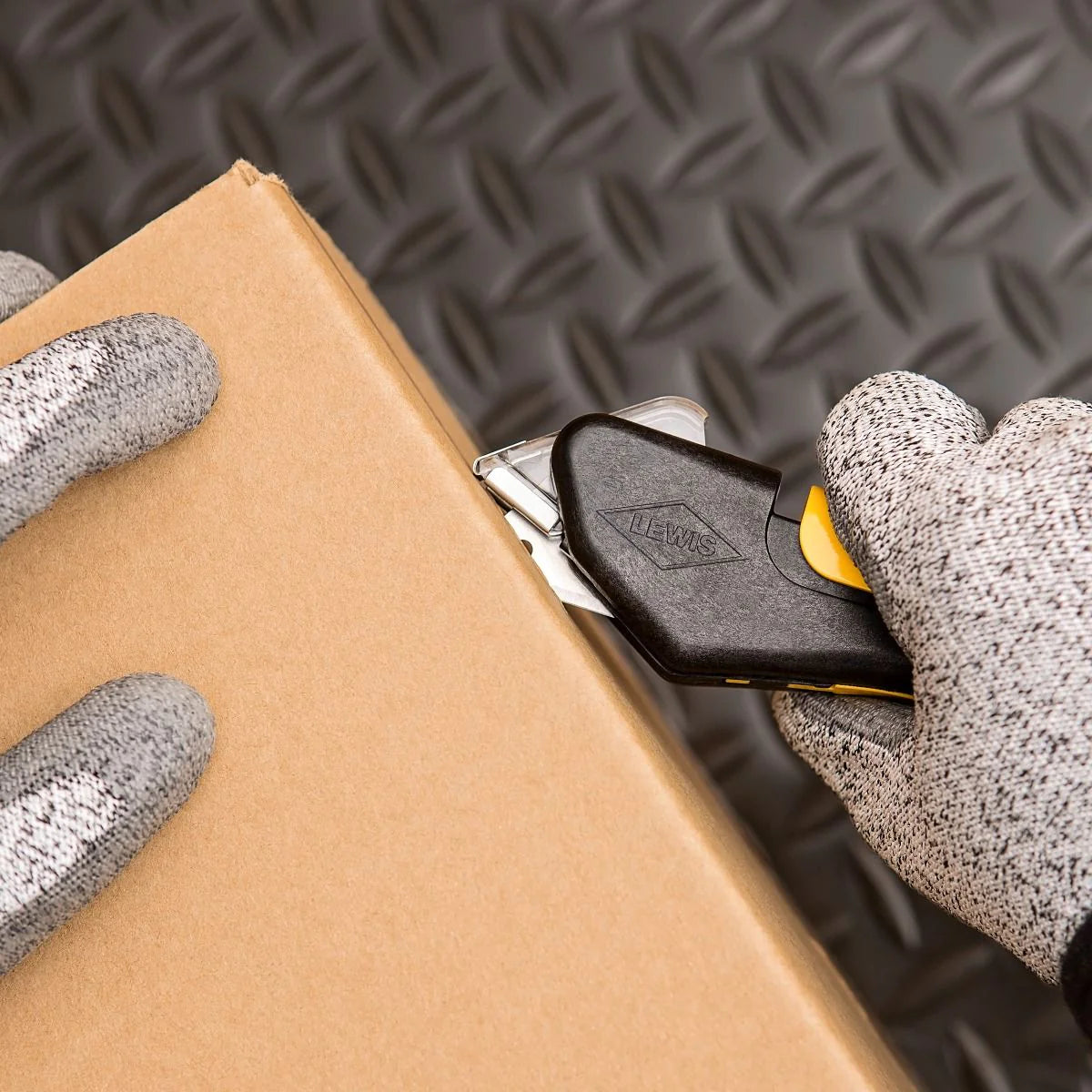
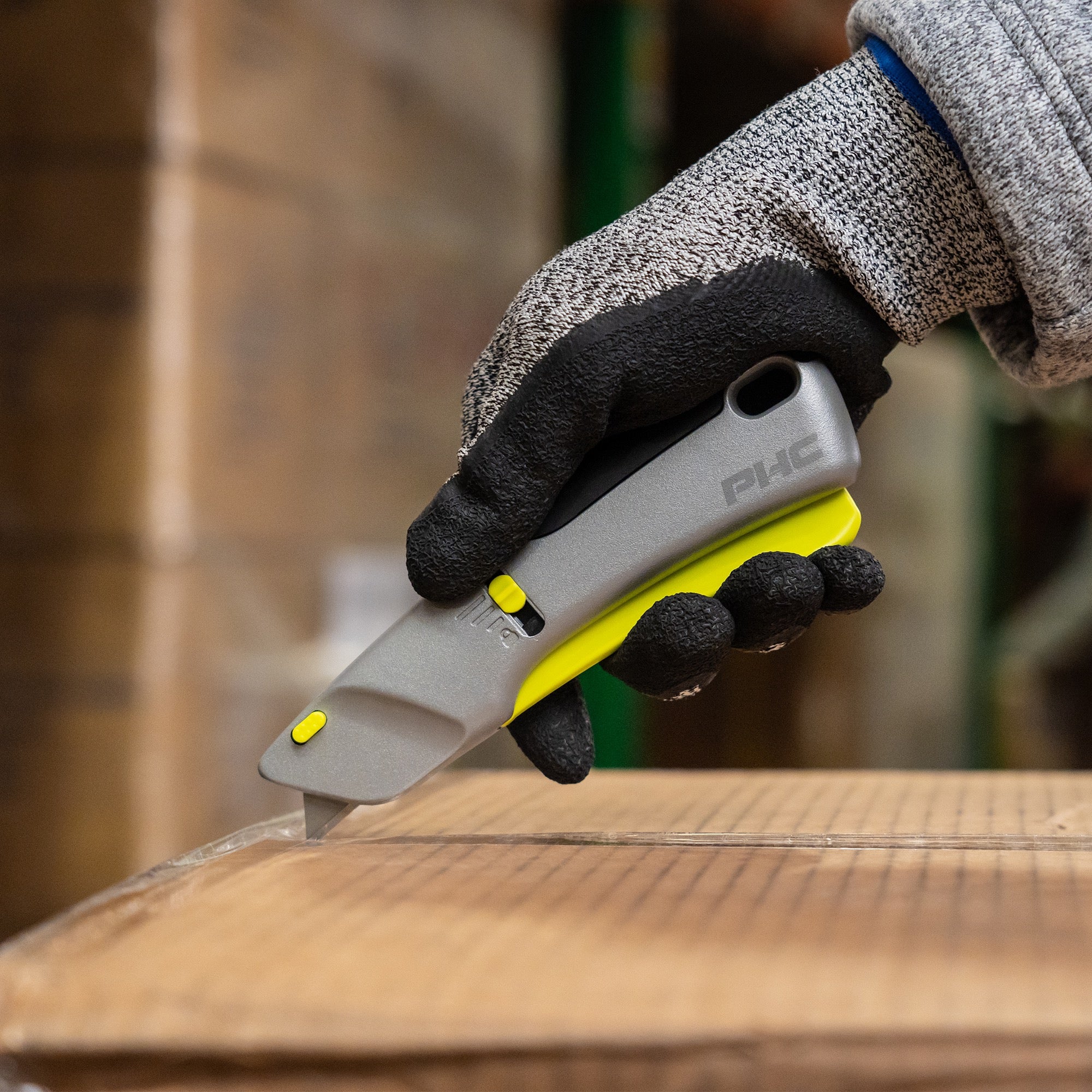
Book a Knife Audit
Ready to improve safety and efficiency in your workplace? Book your Knife Audit today and ensure your team is equipped with the safest, most effective cutting tools.